The Originally posted spindle bearing modification:
When I face my products I cannot tolerate spindle wander, because it produces bands on the finished surface as the spindle floats under varying loads and belt conditions. As posted, here is the low cost (McMaster-Carr) radial needle thrust bearing and hardened washers installed. Set end play to a max of 2/10. It'll never get warm, and the little drilling that used to lubricate the OEM fiber washer still furnishes oil to the new bearing.
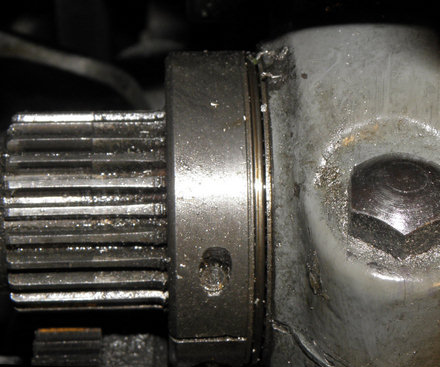
The original back shaft had worn bores in the cast iron housing. I bored and rebushed it with bronze, then added radial needle thrust bearings, as above. Grease fittings were installed. The shaft was replaced with a chromed one. The 6-32 setscrew is for a thermocouple well that I used to monitor breakin. It runs very cool now.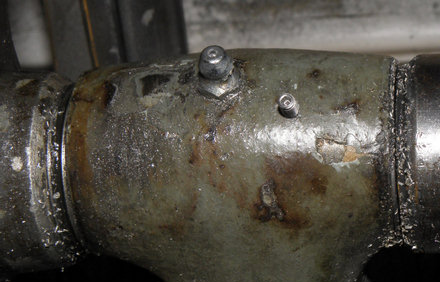
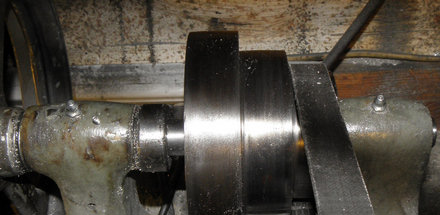
Flying reverse controller, housing and heat sink. Drives a 1 HP Baldor PMDC motor. I use this type of motor on my miller, also. Cool running, variable speed, reversible, and torque regulated...What's not to like?

I made a vacuum chuck. It was the only realistic way of maching my parts and assuring front to back plane parallelism. The hollow quill shaft serves nicely as a vacuum pipe.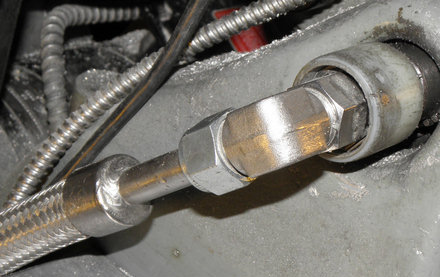
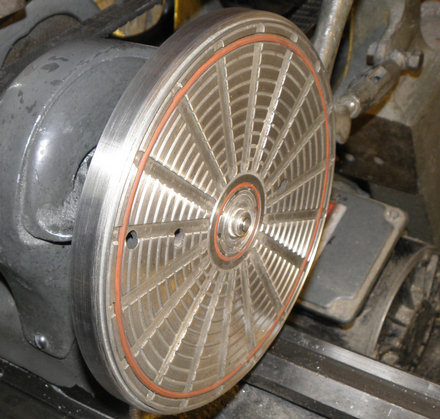
An earlier feeble 3/4 HP PMDC motor is visible in the second picture.
I make hundreds of units at a session. I have better things to do than turn the crossfeed crank to run the tool back out for the next pass. 24 V. PMDC Gearmotor. Tbe crossfeed screw was bored .2495 and a dowel pin pinned in place. this extension attached to the motor coupling. the motor mounting ears float on 2 10-32 screws tapped into the cast iron. 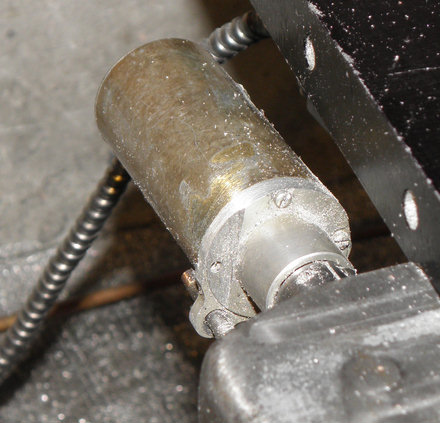
I must mention here that the crossfeed screw has been equipped with a ball bearing. a 3/8 R6 just fits. Unscrew and bore the handle bearing 7/8 Dia, 1/4 deep to accept a 3/8. Bond the bearing into the cleaned and degreased bore, and the bearing ID to the crossfeed screw with an high strength epoxy. This way, it can be easily disassembled by heating to 100°C. It had never failed..the epoxy is a valid way to assemble this.
Running a machine without a DRO is like sex without a partner. You can do it, but it really IS better the other way. Here is the attachment for the Jenix Y encoder:
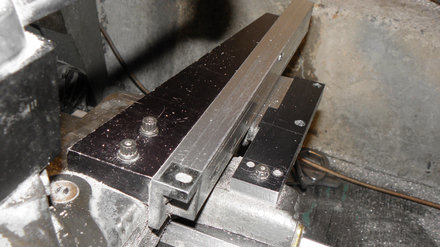